Zone melting and purification
This method does not use crucibles, so it can largely protect the product from contamination by the crucible.
The process of zirconium zone smelting and purification generally includes three stages: raw material preparation, zone smelting and product quality inspection.
Stage 1 Prepare raw materials
The sponge zirconium or zirconium iodide is made into rods by electron beam melting, extrusion, machining and other steps.
Stage 2 Zone smelting
Fix the zirconium rod vertically in the vacuum chamber, use the high-frequency induction coil (or electron gun) as the heat source to melt one end of the rod into a melting zone, and then slowly move the melting zone from one end to the other.
Zirconium is a high melting point metal with strong chemical activity. The vapor pressure at its melting point of 2125K is low, and zone smelting is easier to carry out at this time.
The main factors affecting this stage are the purity of raw materials, vacuum pressure, zone melting speed and zone melting times.
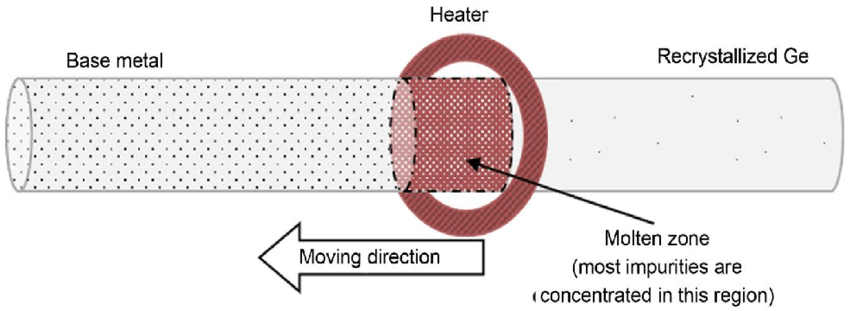
Stage 3 Inspect Product Quality
The head and tail sections of the zirconium rod obtained in the previous stage were excised for sampling. Its various parameters are measured by mass spectrometry, hardness determination or specific resistance.
E-beam melting and purification
Zirconium has a great affinity for oxygen and nitrogen, and 0.2% nitrogen or oxygen in zirconium becomes brittle, making it difficult to process into materials. In this method, the metal to be purified is bombarded with electrons in a vacuum to melt it. In the purification process, in addition to avoiding the oxidation and nitridation of zirconium, the gas dissolved in the zirconium can also escape, the mixed oxide can be decomposed or evaporated, and metal impurities (such as copper, aluminum, gold, iron, manganese, chromium, etc.). The processing properties, electrical properties, magnetic properties and mechanical properties of the zirconium ingot purified by electron beam smelting are obviously better than the raw zirconium.
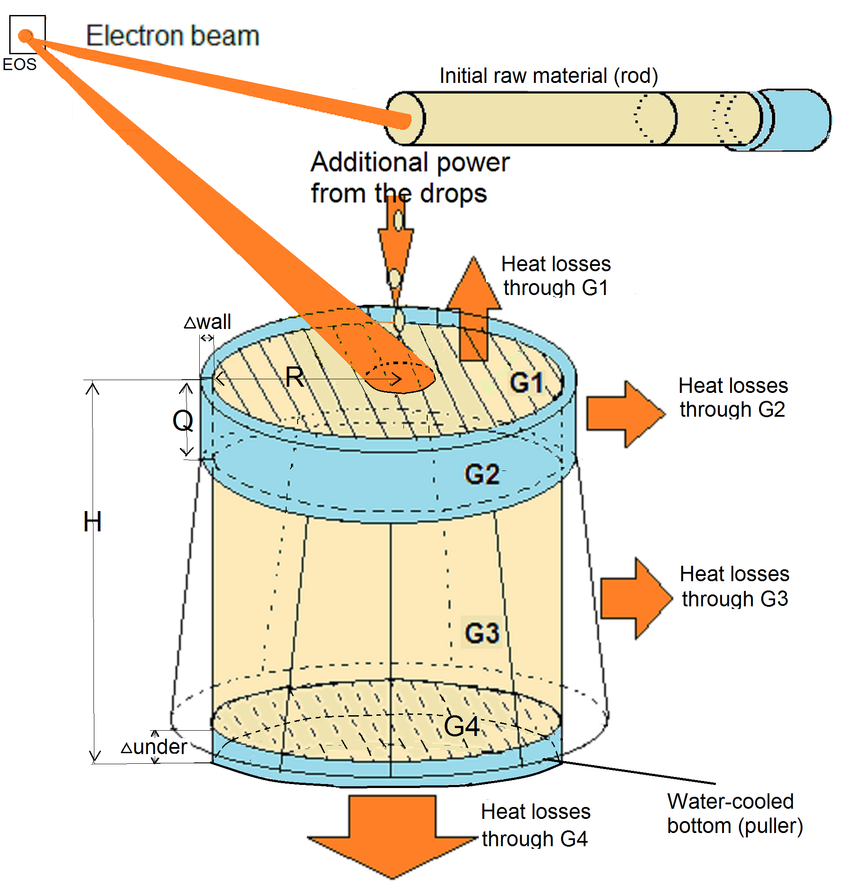
An electron beam melting furnace is composed of an electron gun system, furnace body, vacuum system, raw material adding system, mold mechanical device, operation control system, and high voltage power supply device. The larger the scale is, the lower the product smelting cost is. At present, the smelting process is developing into a semi-continuous or continuous production mode to improve production efficiency and production capacity.
The quality of zirconium ingot purified by electron beam melting depends on the raw material, the melting speed, and the power of the melting furnace.
For more information, please visit www.samaterials.com.