Introduction
Hafnium is a lustrous, silvery metal. It is notable for its remarkable corrosion resistance and its ability to absorb neutrons. Therefore, it is invaluable in nuclear reactors. However, when drawn into wire, it serves various high-tech and industrial applications.
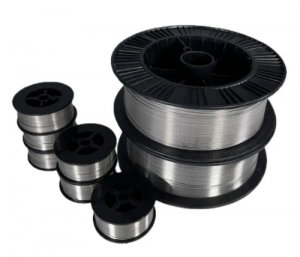
The hardness of hafnium wire is a critical attribute. It determines its wear resistance, durability, and applicability in different environments. It is influenced by several factors, including its composition, diameter, and intended applications.
This article delves into these influencing factors. Hope that you can learn about the efficiency of hafnium wire in diverse applications.
Composition: The Cornerstone of Hardness
The composition of hafnium wire plays a pivotal role in its hardness. Pure hafnium itself exhibits a certain level of hardness, but this can be significantly altered by the presence of impurities or the intentional addition of alloying elements.
Trace elements such as oxygen, nitrogen, and carbon, even in small amounts, can affect the metal’s crystal structure, thereby influencing its mechanical properties. For instance, oxygen can enhance the hardness of hafnium by creating oxygen-stabilized phases within the metal’s structure.
Moreover, alloying hafnium with other metals can tailor its hardness to specific needs. For example, adding zirconium can increase its strength and hardness due to the similar atomic size and chemical properties of the two elements. This alloying practice is common in applications requiring materials that can withstand high temperatures and aggressive environments.
Diameter: A Direct Impact on Hardness
The diameter of hafnium wire is another critical factor influencing its hardness. As the wire is drawn to smaller diameters, it undergoes work hardening, a process that rearranges the metal’s crystal structure, resulting in increased hardness and strength. This phenomenon is attributed to the dislocation movements within the crystal lattice.
This structure becomes more restricted as the wire is drawn thinner, leading to an accumulation of dislocations and an increase in hardness.
However, there is a trade-off between the diameter and the wire’s flexibility. While thinner wires exhibit higher hardness and tensile strength, they may also become more brittle, reducing their ductility. This balance between hardness and ductility is crucial in applications where the wire must endure bending or coiling without fracturing.
Applications: Dictating the Required Hardness
The intended application of hafnium wire significantly influences the desired balance of hardness and other mechanical properties.
–Aerospace:
In the aerospace industry, for example, hafnium wire is used in the manufacture of jet engine components. That’s because high hardness and temperature resistance are essential for withstanding the extreme conditions of jet propulsion systems.
–Nuclear:
Similarly, in nuclear technology, hafnium stands out for its neutron-absorption capability. So, it is ideal for control rods, where hardness contributes to the material’s longevity and reliability in a radioactive environment.
–Others:
Conversely, in applications such as filaments for electronic devices, a moderate level of hardness is preferred to ensure adequate flexibility for shaping and coiling the wire. This demonstrates how the application dictates the specific requirements for hardness, influencing the choice of composition and processing methods to achieve the desired properties.
Processing Techniques and Their Influence
The manufacturing process of hafnium wire, including melting, alloying, and drawing, significantly impacts its final hardness.
- The conditions under which hafnium is melted and cast can introduce or eliminate impurities, affecting the metal’s purity and, consequently, its hardness.
- The drawing process, involving repeated stretching and annealing cycles, can be precisely controlled to achieve the desired wire diameter and hardness.
- Annealing, in particular, allows for adjustments in the wire’s microstructure, reducing or increasing hardness as required by the application.
Future Directions and Innovations
Advancements in material science continue to explore new alloying elements and processing techniques to enhance the properties of hafnium wire.
- Innovations in additive manufacturing, such as 3D printing with metal powders, open new avenues for customizing the composition and microstructure of hafnium alloys. Such development potentially leads to wires with unprecedented hardness and performance characteristics.
- Moreover, research into surface treatments and coatings could offer ways to further increase the wear resistance and hardness of hafnium wire without compromising its intrinsic properties.
- These developments hold promise for expanding the applications of hafnium wire beyond its current uses. They leverage its unique combination of hardness, corrosion resistance, and neutron absorption capability.
Conclusion
The hardness of hafnium wire is a complex interplay of composition, diameter, and application requirements. Each factor intricately influences the material’s performance and suitability for specific uses.
Through careful selection of alloying elements and precise control over the manufacturing process, it is possible to tailor the hardness of hafnium wire to meet the demands of various high-tech and industrial applications.
As research and technology continue to advance, the potential for new hafnium alloys and applications seems boundless. For more information related to hafnium wires, please check our homepage.