Zirconium alloys have a small thermal neutron capture cross-section (0.185b) and are surprisingly resistant to corrosion, so they are widely used in fission reactors, such as core-clad tubes, grids, and guide tubes in boiling water reactors, as well as pressure pipes and exhaust reactor vessels in pressurized water reactors.
Nuclear zirconium alloy
With the application of zirconium alloys in the nuclear energy industry, the zirconium industry has developed rapidly.
In the nuclear giant change reactor, nuclear fuel is fission reaction all the time. In the reaction, the neutron bombards the nucleus of U235, which splits into Ba140 and Kr93, and releases two or three neutrons at the same time; other U235 nuclei are bombarded by these neutrons and re-fission. This is the chain reaction of fission.
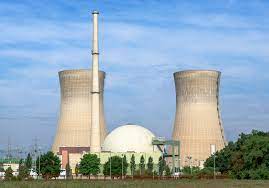
A material with a large neutron capture cross-section will absorb many neutrons when they hit the wall, reducing the efficiency of the chain reaction. Meanwhile, the chain reaction produces a lot of heat, which is removed by circulating cooling water (or other coolants) to avoid overheating and damage to the reactor. When metals come into contact with high-temperature water, they can be corroded (oxidized). Materials with poor corrosion resistance need to be replaced frequently, which increases the cost and easily leads to safety accidents. Therefore, as core-cladding and structural materials, zirconium alloys are required to have low neutron capture cross-section and excellent corrosion resistance, so the development of zirconium alloys should be attributed to the nuclear industry.
Origin of zirconium alloys
Initially, zirconium was not considered a suitable material for use in the nuclear industry, because studies have shown that zirconium’s effect on thermal neutron absorption can affect the efficiency of nuclear reactors. Later, researchers at the Oak Ridge Institute found that 2.5% of the hafnium in zirconium was responsible for its large thermal neutron capture cross-section.
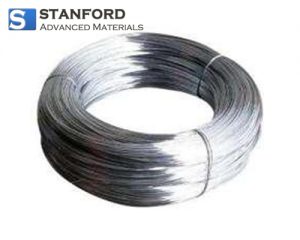
Zirconium and hafnium are associated with ore and are generally difficult to separate. Until the 1850s, Admiral in the Naval Nuclear Propulsion project decided to use zirconium in the water-cooled reactor of the Nautilus Nuclear Submarine. Although zirconium had already been used for the project by that time, there were no strict standards for the use of zirconium, and the researchers only knew that improving the purity of zirconium would be good for the properties of the alloy. Some processes are used to purify strip zirconium, but it still contains small amounts of nitrogen, making it less resistant to corrosion at high temperatures. Finally, the researchers realized that purity was not the key to zirconium’s corrosion resistance, because they found that some zirconium materials containing impurities (such as tin, iron, chromium, and nickel) were more resistant to corrosion than higher-purity zirconium materials. Therefore, the development of zirconium alloys is put on the agenda.
Development of zirconium alloys
The first alloy, Zircaloy-1, contains 2.5% tin. It was found that the corrosion rate of Zircaloy-1 alloy was increasing and not consistent with the expected decrease. This was similar to a normal sponge zirconium material, so Zircaloy-1 was quickly abandoned.
At the same time, the researchers found that adding iron and nickel to the Zircaloy-2 could improve corrosion resistance. The tin content was reduced to 1.5% and 0.15% iron, 0.05% nickel and 0.10% chromium were added. It was found that Zircaloy-2 had the same mechanical properties as Zircaloy-1, but the high-temperature corrosion resistance of Zircaloy-2 was much better than that of Zircaloy-1. However, during the service of the pressurized water reactor, the alloy produces a lot of hydrides, resulting in hydrogen embrittlement.
By studying the binding technique, the researchers found that nickel greatly enhanced the hydrogen absorption capacity of zirconium alloys. The researchers removed the nickel from the Zircaloy-2, creating a Zircaloy-3. But Zircaloy 3 was quickly abandoned because its strength was too low. In addition, Zircaloy-3 produced many striated Fe-Cr binary intermetallic compounds when it was processed in the two-phase zone, so it could not provide sufficient corrosion resistance. The strength of Zircaloy-3 was still too low, although changes in the heat treatment process prevented the production of the striated compound.
The researchers compensated for the nickel by increasing the iron content by 0.22 percent and found that the corrosion resistance of the new alloy was similar to that of zircaloy-2, which had only half the hydrogen absorption rate. The new alloy quickly became a major part of the pressurized water reactor, the first Zircaloy-4.
Zirconium alloys for the nuclear industry have been developed into the third generation of products, which are used in various reactors.
The first generation is the standard zircaloy-4 and Zircaloy-2, whose composition and process requirements are specified in the ASTM standard. This generation of zirconium alloy is still in use.
The second generation is low tin Zircaloy-4 and optimized Zircaloy-4. The tin content of low tin Zircaloy 4 decreased from 1.2% ~ 1.70% to 1.20% ~ 1.50%, and the carbon and silicon were controlled at 0.008% ~ 0.020% and 0.005% ~ 0.012%, and the cumulative annealing process parameters in the alpha phase after quenching in the beta phase were strictly controlled; the optimized zircaloy-4 is based on the low tin zircaloy-4, and the content of alloy elements and process parameters are more strictly controlled, so as to improve the uniformity of materials.
The third generation of zirconium alloy has excellent properties and is widely used as a fuel rod cladding tube and fuel assembly guide tube. NDA and MDA from Japan, HANA from South Korea, and composite casings from Siemens are also examples of this generation of products.
Prospect of zirconium alloys
Zirconium alloys above 620℃ (depending on composition) convert to body-centered cubic β-zirconium. After the transformation, the mechanical properties and corrosion resistance of the alloy will be greatly reduced, and it cannot continue to maintain the safe operation of the nuclear reactor. The famous event is the accident at the Fukushima nuclear power plant in Japan. Affected by the big earthquake in eastern Japan, the reaction water of the Fukushima nuclear power plant leaked, and the cladding temperature increased significantly. The zirconium alloy cladding softened quickly, and brittle material formed with the leakage of air, leading to the leakage of nuclear fuel. Large amounts of nuclear-contaminated water flowing into the sea have caused great damage to the ecology of the world.
As a nuclear reactor cladding material, it needs to have a small thermal neutron capture cross-section, which leads to the zirconium alloy cannot be highly alloyed, so it is bound to be difficult to break through the zirconium alloy’s high-temperature performance. At present, countries attach great importance to this problem. On the one hand, they are trying their best to make a breakthrough in the high-temperature performance of zirconium alloy; on the other hand, they are looking for alternative products of existing fuel cladding, such as silicon carbide (SiC) composite material, molybdenum alloy, cobalt alloy and so on. Molybdenum alloys and cobalt alloys were originally intended as structural materials for fusion reactors. Although they do not have the same low thermal neutron absorption cross-section as zirconium alloys, they have excellent high-temperature stability.
Stanford Advanced Materials supplies high-quality zirconium alloys to meet our customers’ R&D and production needs. Please visit http://www.samaterials.com for more information.