Zirconia is a kind of inorganic nonmetallic material with high-temperature resistance, corrosion resistance, abrasion resistance, and excellent electrical conductivity. Since the mid-1970s, developed countries have invested heavily in the research and development of zirconia products, extending the application field of zirconia to structural and functional materials. Zirconia is also one of the new high-performance materials in the national industrial policy, which is widely used in various industries.
Applications of zirconia in structural ceramics
In 1975, R.G.Garvie, Australia, prepared partially stabilized zirconia with calcium oxide as a stabilizer, and improved the toughness and strength of zirconia for the first time, which greatly expanded its application in the field of structural ceramics.
1. Zirconia ceramic bearings
Zirconia ceramic bearing has the characteristics of wear resistance, corrosion resistance, high-temperature resistance, high cold resistance, oil-free self-lubrication, resistance to magnetoelectric insulation, etc. It can be used in an extremely harsh environment and under special working conditions.
Zirconia ceramic bearings have been used in micro cooling fans, and the product life and noise stability are better than traditional ball and sliding bearing systems. Foxconn is the first company to use zirconia ceramic bearings in computer cooling fans.
2. Zirconia ceramic valve
At present, valves commonly used in various industries are made of metal materials. Due to the limitation of metal material itself, the corrosion damage of metal has a considerable impact on the working life, reliability and service life of valve wear resistance.
The working climate of the valve pipeline is very complicated. Hydrogen sulfide, carbon dioxide, and some organic acids in oil, gas, and reservoir water increase the destructive power of their surfaces, rapidly disabling them. Zirconia ceramic valve has excellent wear resistance, corrosion resistance, high-temperature resistance, and thermal shock resistance, so it is suitable for this field.
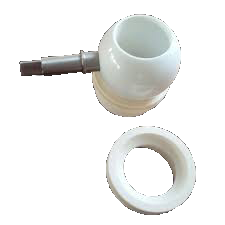
3. Zirconia abrasive material
Zirconia ball has the advantages of high hardness, low wear rate and long service life, which can greatly reduce the pollution of grinding materials and ensure the quality of products. Besides that, zirconia material has high density and strong impact energy when used as a grinding medium, which can greatly improve the grinding dispersion efficiency. Good chemical stability determines its corrosion resistance and can be used in acidic and alkaline media.
Applications of zirconia in functional ceramics
1. Zirconia ceramic knives
Zirconia ceramic knife has the characteristics of high strength, wear resistance, no rust, no oxidation, acid and alkali resistance, anti-static, and no reaction with the food. Its body is as shiny as jade, which also makes it an ideal high-tech green knife. At present, the main products on the market are zirconia ceramic knife, scissors, razor, scalpel and so on, which has become popular in Europe, America, and Japan in recent years.
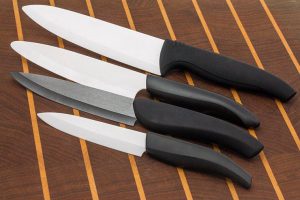
2. Zirconia high-temperature heating element
Zirconia is an insulating material at room temperature, its resistivity is as high as 1015 Ω cm, and it can conduct electricity when the temperature to 600 ℃. When the temperature reaches 1000℃ above, it is a good conductor and can be used as 1800℃ high-temperature heating element, with the highest operating temperature of 2400℃. At present, zirconia has been successfully used in heating elements and equipment with an oxidation atmosphere above 2000℃.
3. Zirconia bioceramics
The quality of ceramic tooth material directly affects its quality and patients’ health. The inner crown of porcelain teeth is made of different metal materials, which is easy to oxidize with saliva. Since there is no metal inner canopy, zirconia ceramic teeth have good transparency, excellent gloss, and effectively avoid tooth allergies and gum black lines.
4. Zirconia coating material
Zirconia thermal barrier ceramic coating material with a high-performance stabilizer such as yttrium oxide (Y2O3) is mainly used in high-performance turbine aero-engine. The thermal barrier coating uses ceramic insulation and corrosion resistance to protect the metal material, which can not only improve the fuel combustion efficiency but also greatly extend the life of the engine. Thermal barrier coating has important application value in aviation, aerospace, surface ships, large thermal power generation, and automobile power, etc. It is one of the most important technologies in modern national defense.
5. Zirconia oxygen sensor
Oxygen sensors are essential in the automotive industry for engines that use three-way catalytic converters to reduce pollution emissions. Currently, there are two kinds of oxygen sensors in use: titanium oxide and zirconia. Japanese scientists made a porous oxygen sensor out of zirconia, which is installed in an engine to automatically detect the ratio of oxygen to combustion gas in the engine, and automatically control the ratio of input gas and output gas, thus greatly reducing the harmful gas emissions from cars.
Stanford Advanced Materials supplies high-quality zirconia ceramic products to meet our customers’ R&D and production needs. Please visit https://www.samaterials.com for more information.